www.industry-vietnam.com
11
'09
Written on Modified on
Amiantit
FLOWTITE™, GRP pipe systems for water, sewage and industrial applications
FLOWTITE technology has been developed to provide many industries all around the world with low cost, long term piping solutions. They are 10 times lighter than a concrete pipe, as well as easy to handle and install. These GRP Pipe systems are corrosion-free and have a proven resistance to acidic environments.
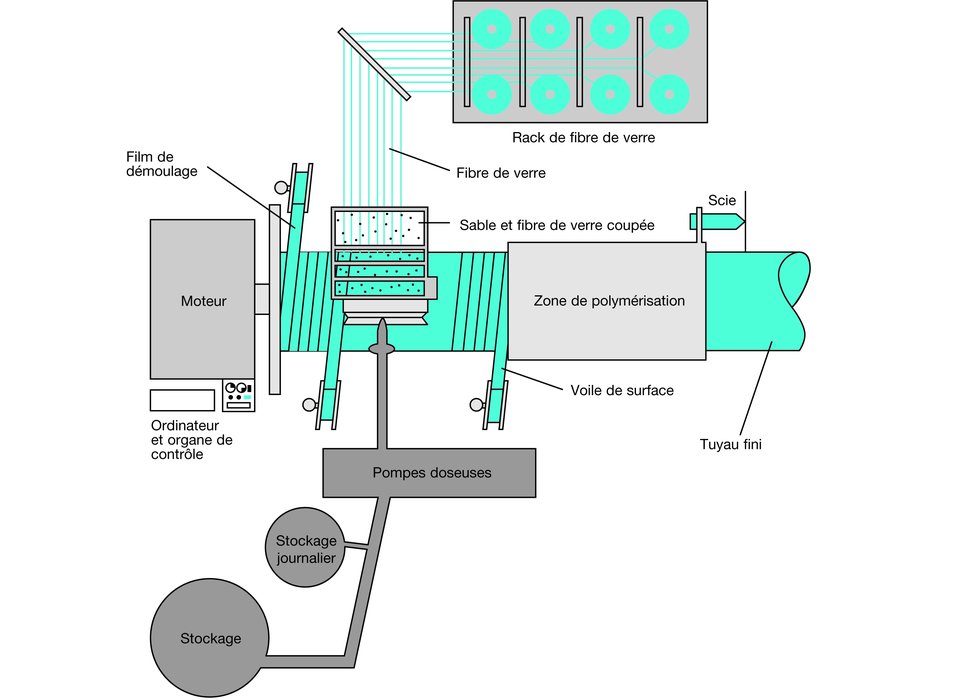
FLOWTITE GRP (Glass Reinforced Polymer) pipe systems are highly resistant to corrosion. They are durable and have low maintenance costs. There is no need for linings, coatings, cathodic protection, wraps or other types of extra corrosion protection.
These outstanding features are permitted by an advanced design and manufacturing process. The main basic raw materials used in the manufacturing process are resin, fibreglass and silica sand.
FLOWTITE pipes are manufactured using the continuous advancing mandrel process, which is the state of the art in GRP pipe production. The process allows the use of continuous glass fibre reinforcements in the circumferential direction. For a pressure pipe or buried conduit the principal stress is in the circumferential direction. Incorporating continuous reinforcements in this direction yields a higher performing product at lower cost. It creates a very compressed laminate, which maximizes the contribution from the three basic materials. Both, continuous glass fibre rovings and choppable roving, are incorporated for high hoop strength and axial reinforcement. A sand fortifier provides increased stiffness by adding extra thickness, placed near the neutral axis in the core.
These outstanding features are permitted by an advanced design and manufacturing process. The main basic raw materials used in the manufacturing process are resin, fibreglass and silica sand.
FLOWTITE pipes are manufactured using the continuous advancing mandrel process, which is the state of the art in GRP pipe production. The process allows the use of continuous glass fibre reinforcements in the circumferential direction. For a pressure pipe or buried conduit the principal stress is in the circumferential direction. Incorporating continuous reinforcements in this direction yields a higher performing product at lower cost. It creates a very compressed laminate, which maximizes the contribution from the three basic materials. Both, continuous glass fibre rovings and choppable roving, are incorporated for high hoop strength and axial reinforcement. A sand fortifier provides increased stiffness by adding extra thickness, placed near the neutral axis in the core.
With the FLOWTITE dual resin delivery system, the equipment can apply a special inner resin liner for highly corrosive applications. A standard resin can still be used for the structural and outer portion of the laminate. Taking advantage of the winding process, other materials – such as a glass or polyester veil – can be used to enhance abrasion and chemical resistance in the finished pipe.
The FLOWTITE filament-winding machine represents the most advanced technology in use, and is the leading method for manufacturing glass fibre pipe. It consists of a continuous steel band mandrel supported by beams in a cylindrical shape. As the beams turn, friction pulls the steel band around and a roller bearing allows the band to move longitudinally. The entire mandrel then moves continuously in a spiral path towards the exit assembly. As the material rotates, all composite materials are metered onto it in precise amounts. Electronic sensors provide continuous production parameter feedback so that the various feeding systems apply the right amount of material needed to build the different layers is applied throughout the manufacturing stage. Firstly, mould-release film, followed by various forms and patterns of glass fibres, embedded in a polyester resin matrix. The structural layers are made of glass and resin only, whereas the core layer includes pure silica. It is the continuous application of these materials onto the mandrel that form the pipe.
Applications
FLOWTITE fibreglass pipes and fittings are used in many applications. They can be found in the delivery of drinking water, in sewage applications and irrigation, in fire-fighting, sea and desalinated water, in power plants, as well as.in chemical and industrial wastes The use of FLOWTITE pipe systems is virtually unlimited. You find the products in siphon lines as often as you do in seawater outfalls, bridge dewatering and desalination projects. It can be also utilised as protection lines for cables.
Main features
With diameters ranging from DN100 to DN4000 mm, the pipes are supplied in standard lengths of 6 and 12 metres. Customized lengths up to 18 metres are available on request. Diameters of less than DN300 mm are available in standard lengths of 6 metres.
The maximum standard pressure is 32 bar, depending on diameter and the maximum stiffness is 10,000 N/m2.
FLOWTITE fibreglass pipes and fittings are used in many applications. They can be found in the delivery of drinking water, in sewage applications and irrigation, in fire-fighting, sea and desalinated water, in power plants, as well as.in chemical and industrial wastes The use of FLOWTITE pipe systems is virtually unlimited. You find the products in siphon lines as often as you do in seawater outfalls, bridge dewatering and desalination projects. It can be also utilised as protection lines for cables.
Main features
With diameters ranging from DN100 to DN4000 mm, the pipes are supplied in standard lengths of 6 and 12 metres. Customized lengths up to 18 metres are available on request. Diameters of less than DN300 mm are available in standard lengths of 6 metres.
The maximum standard pressure is 32 bar, depending on diameter and the maximum stiffness is 10,000 N/m2.