www.industry-vietnam.com
02
'10
Written on Modified on
Remform and ATP screws
Arnold provides two new reliable and cost-effective assembly methods to answer to the continuously evolving use of plastics. Remform screws is a solution for detachable plastic parts joints whereas Arnorld Tripress (ATP) are dedicated to permanent joints for ductile light metals or plastics.
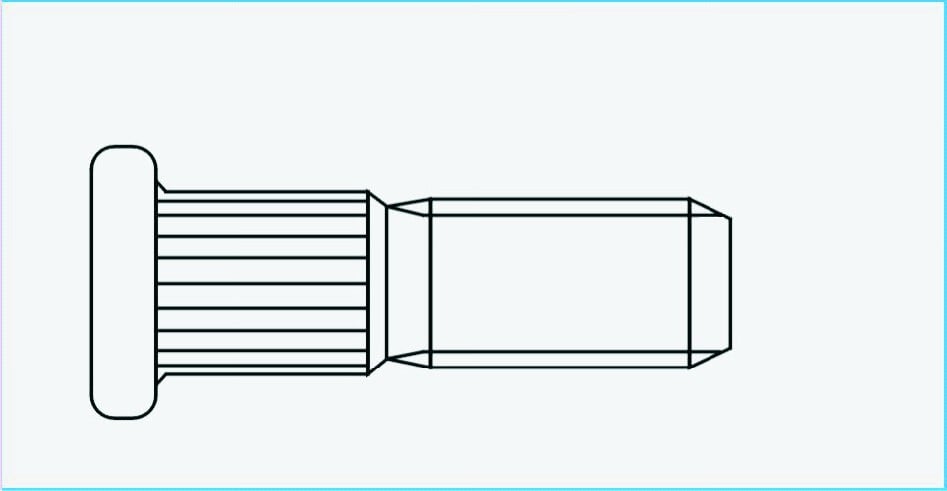
Remform screws for detachable joints
Joints of this type are usually formed using bolts and nuts. It requires a significant amount of assembly time. The most economical option for fulfilling these extensive requirements is to use Remform screws for direct assembly with plastics. This form of threaded fastener assembly minimises the overall cost because the use of direct assembly technology with plastics eliminates operations such as fitting inserts. Thanks to the asymmetric flanks of the thread profile, Remform screws give the entire joint high operational reliability. The asymmetric thread geometry of the screw optimises the material flow of the thread formed in the plastic and increases the pull-out force compared to conventional symmetric thread flanks. Remform provides high assembly process reliability due to the large differential between the screw-in torque and the stripping torque, along with high dynamic load capacity due to the reinforced thread core cross-section.
As Arnold Umformtechnik recently demonstrated with the use of Remform screws by a renowned manufacturer of washing machines, this is more than just abstract theory. The customer’s requirements involved the assembly of a two-piece washing machine outer drum, which required fulfilling the following parameters:
- The residual clamp force must remain at an adequate level for the lifetime of the washing machine in order to ensure the leak-tightness of the drum
- Operating temperature range of -10° to +65° C
- Extremely short assembly time (less than 1 second per screw)
- Vibration resistance
Arnorld Tripress for permanent joints
Permanent joints are most often made by welding, gluing, riveting or clipping. Although these methods ensure that the parts cannot become separated, they are often expensive in practice. For this reason, Arnold has developed the Arnold Tripress (ATP), a fastener that can be used to produce a detachable or permanent joint, or even a combination of the two. Unlike conventional products with round shanks, they have a trilobular (triangular) cross-section. When the stud is pressed into a round core hole, the hole deforms and takes on the trilobular shape of the stud. The resulting form fit minimises the pressing force. After the stud is pressed in, considerable torque or tensile force is necessary to dislodge it – far more than the yield torque of a conventional fastener. ATP fasteners can be pressed into ductile light metals and plastics.
These fasteners are of course suitable for a wide variety of applications, but their advantages really stand out for securing electrical terminals in motor vehicles. These terminals are conventionally designed to be secured with standard hex screws in order to distribute the torque arising from the attached connecting wire over the mating surface of the component. The fastener or terminal stud is fitted separately.
Considerable savings in tooling costs can be achieved by using the ATP fastener system. The appropriate fastener is pressed in until the head is flush with the surface, with no need for complex tooling or additional parts. After the ATP fastener is pressed in, the threaded portion protrudes from the component. The part to be attached is fitted over the protruding end and secured with a tightened nut.
Joints of this type are usually formed using bolts and nuts. It requires a significant amount of assembly time. The most economical option for fulfilling these extensive requirements is to use Remform screws for direct assembly with plastics. This form of threaded fastener assembly minimises the overall cost because the use of direct assembly technology with plastics eliminates operations such as fitting inserts. Thanks to the asymmetric flanks of the thread profile, Remform screws give the entire joint high operational reliability. The asymmetric thread geometry of the screw optimises the material flow of the thread formed in the plastic and increases the pull-out force compared to conventional symmetric thread flanks. Remform provides high assembly process reliability due to the large differential between the screw-in torque and the stripping torque, along with high dynamic load capacity due to the reinforced thread core cross-section.
As Arnold Umformtechnik recently demonstrated with the use of Remform screws by a renowned manufacturer of washing machines, this is more than just abstract theory. The customer’s requirements involved the assembly of a two-piece washing machine outer drum, which required fulfilling the following parameters:
- The residual clamp force must remain at an adequate level for the lifetime of the washing machine in order to ensure the leak-tightness of the drum
- Operating temperature range of -10° to +65° C
- Extremely short assembly time (less than 1 second per screw)
- Vibration resistance
Arnorld Tripress for permanent joints
Permanent joints are most often made by welding, gluing, riveting or clipping. Although these methods ensure that the parts cannot become separated, they are often expensive in practice. For this reason, Arnold has developed the Arnold Tripress (ATP), a fastener that can be used to produce a detachable or permanent joint, or even a combination of the two. Unlike conventional products with round shanks, they have a trilobular (triangular) cross-section. When the stud is pressed into a round core hole, the hole deforms and takes on the trilobular shape of the stud. The resulting form fit minimises the pressing force. After the stud is pressed in, considerable torque or tensile force is necessary to dislodge it – far more than the yield torque of a conventional fastener. ATP fasteners can be pressed into ductile light metals and plastics.
These fasteners are of course suitable for a wide variety of applications, but their advantages really stand out for securing electrical terminals in motor vehicles. These terminals are conventionally designed to be secured with standard hex screws in order to distribute the torque arising from the attached connecting wire over the mating surface of the component. The fastener or terminal stud is fitted separately.
Considerable savings in tooling costs can be achieved by using the ATP fastener system. The appropriate fastener is pressed in until the head is flush with the surface, with no need for complex tooling or additional parts. After the ATP fastener is pressed in, the threaded portion protrudes from the component. The part to be attached is fitted over the protruding end and secured with a tightened nut.